Widely Applied and Expanding its Range Rapidly
The acrylic resin production line encompasses multiple links, starting from raw material storage, batching, polymerization reaction, cooling, separation, all the way to packaging. JCT, with its advanced automated control systems, is committed to helping customers enhance production efficiency, cut down labor costs, and ensure the stable quality of products. This production line is a high - quality solution that meets the needs of various industries.
Product Features
- Wide Range of Applications
It can be applied in various industries such as the coating industry (including architectural coatings, automotive coatings, wood coatings, etc.), the adhesive field (covering paper, packaging, wood, flooring, etc.), ink (especially flexographic printing ink), textiles (improving fabric flexibility, wear resistance and water resistance) and electronic materials (such as electronic packaging materials, printed circuit boards, etc.), demonstrating strong versatility and adaptability.
-
Performance Optimization
In different application fields, it can play corresponding performance advantages targeted, helping to improve the quality and usage effect of corresponding products. For example, it can improve multiple fabric properties in the textile field and meet the usage requirements of relevant materials in the electronic materials field.
Production Line Equipment Configuration
- Base material tank: It is used to store various basic raw materials required for acrylic resin production, ensuring a stable supply of raw materials and laying the foundation for subsequent production processes.
- Monomer emulsion groove: Accurately stores monomer emulsions, ensuring accurate dispensing during the batching process, which helps to guarantee the accuracy and consistency of the product formula.
- Polymerized reactor: One of the core equipment of the production line. The crucial polymerization reaction occurs here. By strictly controlling the reaction conditions, acrylic resin that meets the quality requirements is generated.
- Condenser: Effectively cools the materials after the reaction, ensuring that the temperature during the production process meets the process requirements and facilitating the smooth progress of subsequent separation and other processes.
- Mixing kettle: Thoroughly mixes the materials at different processing stages, further optimizing the uniformity and performance of the product.
- Filter: Can remove impurities generated during the production process, enabling the final product to reach a higher level of purity and meeting the strict quality requirements of various application scenarios.
- Filling machine: Realizes automated product packaging, accurately controlling the filling volume, improving packaging efficiency, and ensuring the standardization of the product packaging process.
- Steam boiler: Provides the required heat energy for the entire production process, ensuring that each link operates under appropriate temperature conditions.
- Water cooling system: Collaborates with equipment such as condensers to efficiently dissipate excess heat, maintaining a stable temperature environment for the production line and ensuring production safety and efficiency.
- Soft water treatment system: Softens the production water, avoiding the impact of impurities in the water on product quality and ensuring high - quality production water.
- Material pump: Responsible for transporting materials at different stages, ensuring the smooth flow of materials between various devices and maintaining the continuous operation of the entire production line.
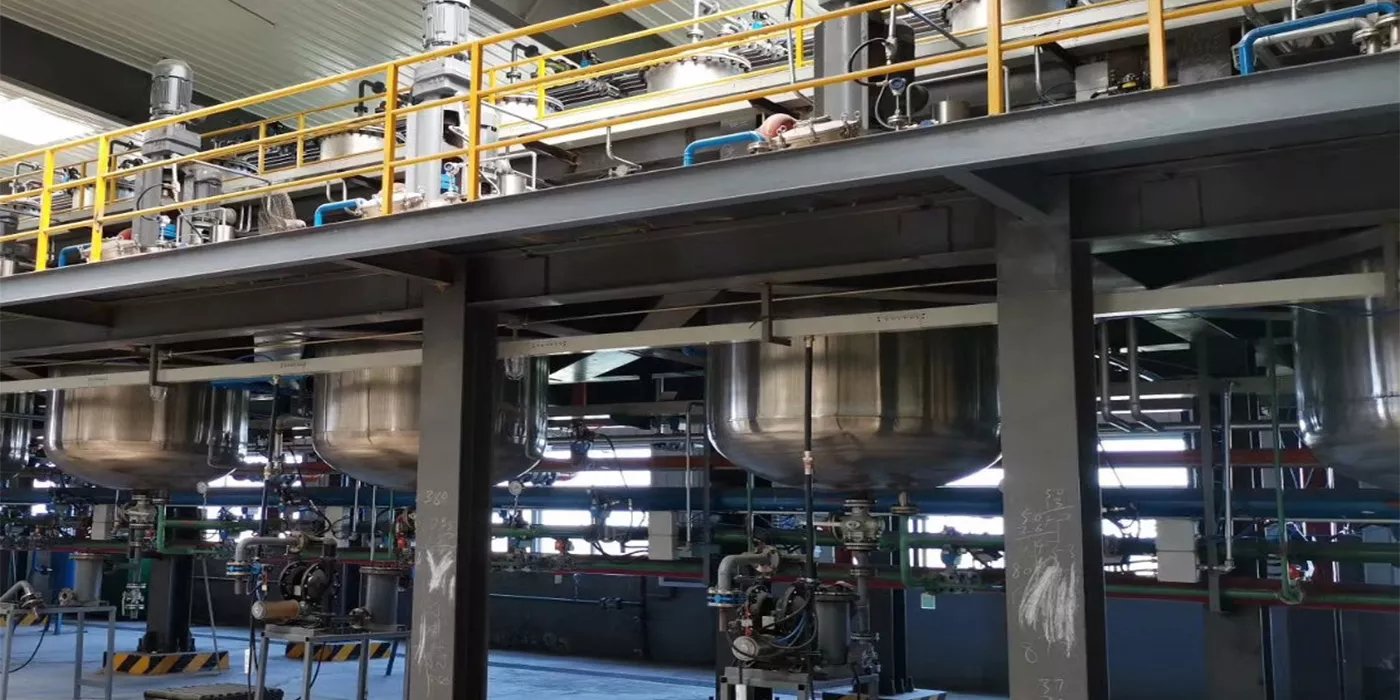
Application Fields
- Coating industry: Widely used in the production of various coatings such as architectural coatings, automotive coatings, and wood coatings, providing high - quality coating solutions for the construction, automotive, and furniture industries.
- Adhesives: Applied to adhesives in fields like paper, packaging, wood, and flooring, meeting the bonding needs of different materials.
- Ink: Used in various printing inks, especially flexographic printing inks, endowing inks with excellent performance.
- Textiles: Applied to textile coatings to enhance the flexibility, wear resistance, and water resistance of fabrics, improving the overall quality of textiles.
- Electronic materials: Used in electronic packaging materials and printed circuit boards (PCBs), contributing to the development of the electronics industry.
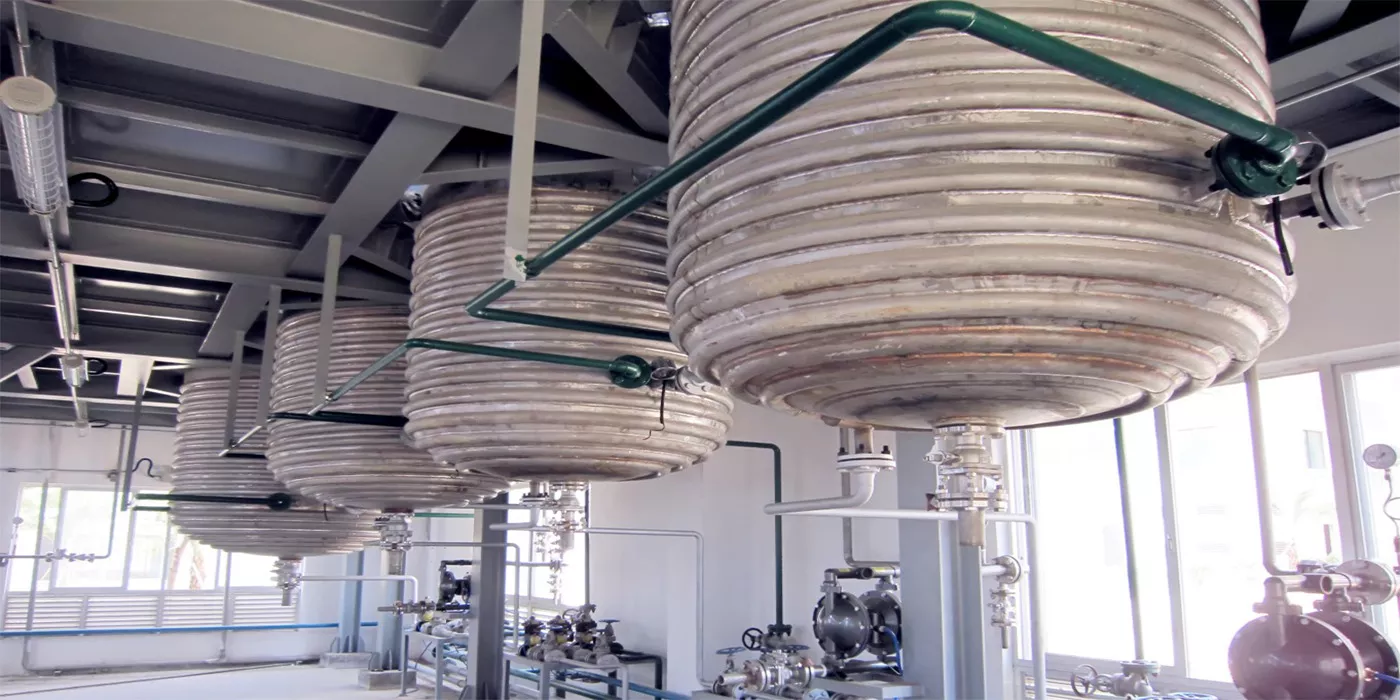
Advantages
- High - efficiency production: The automated control system optimizes each production link, significantly improving production efficiency.
- Cost - saving: Reduces labor costs through automation, and at the same time, the stable operation of the production line reduces production losses, saving costs for customers.
- Quality assurance: Strict control of the production process and high - quality equipment ensure the stable quality of acrylic resin products, meeting the strict requirements of different application fields.
ABOUT JCT
JCT Machinery was founded in 2006. Its business involves mechanical equipment design and manufacturing, intelligent control system research and development, engineering design and installation, etc. The main products include resin synthesis reaction production line, adhesive manufacturing production line, etc., which are widely used. They mainly serve and are used in the fields of fine chemicals, coatings, adhesives, and other fields.
JCT's equipment and production lines have many Patents and areCE-certified. Its customers are spread over more than 30 countries and regions around the world and have been widely recognized and supported by many large and small companies at home and abroad.
JCT has an independent office and factory in Foshan, Guangdong, less than 1 hour's drive from Guangzhou Baiyun International Airport and Guangzhou South High-speed Railway Station. Customers are welcome to come for a face-to-face interview. JCT's sales and engineers will be very willing to have detailed technical communication and discuss optimization technical solutions with you.
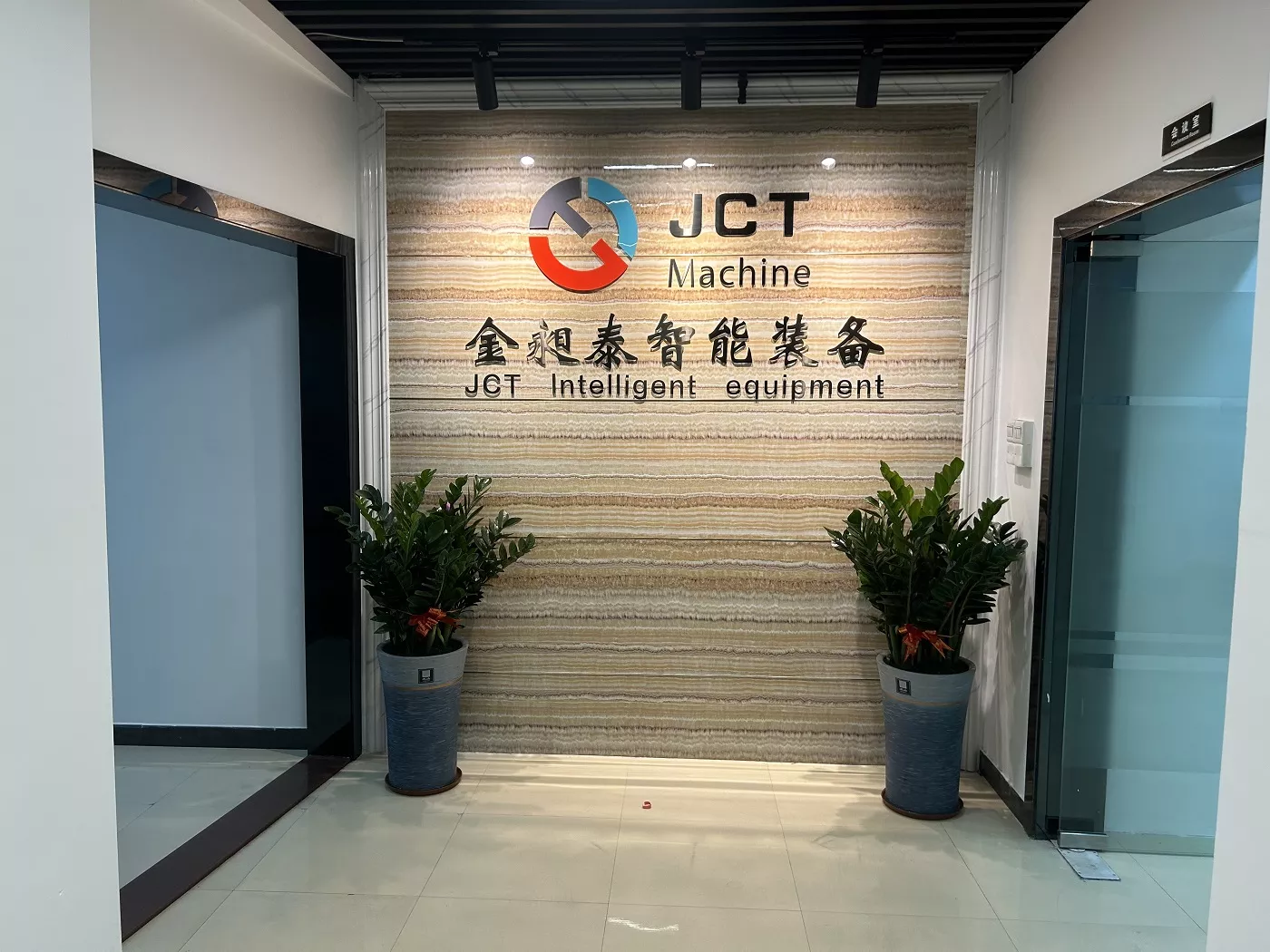
FAQ

Are you a trading company or a manufacturer?

Can you send the formula for the products we want to make?

Can you send the detailed drawings of the machine to us before we place an order?